Molds, Molds and More Molds
Reprinted from "Crown Jewels of the Wire", November 2003, page 14
Tucked away in one of many areas, famous for glass houses, is a cache of
molds. Cast iron molds, that is! While visiting the Museum of American Glass at Wheaton
Village¹ in Millville, New Jersey recently, I was taken by the
bounty of molds arranged in specific eras of history representing a chronology
of innovative ways to press decorative and utilitarian glass of many colors,
sizes and shapes - including insulators.
Most interesting was the innovative process of embossing text and/or designs
onto the glass. This is familiarly referred to as slug plates. Whitall, Tatum
& Co. produced and sold them in their 1880s catalog² as designs for lettered
plates.
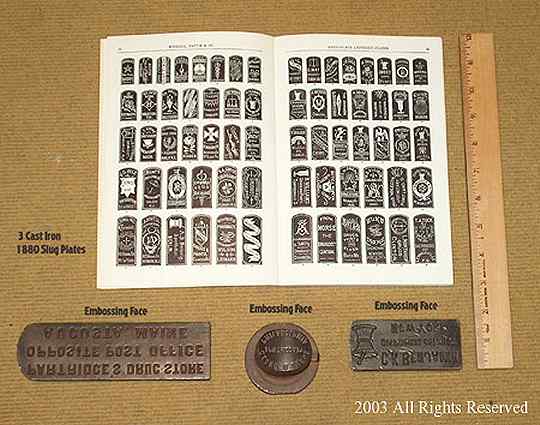
Photographed from the Archives of the Museum of American Glass
Today, molds are essentially made the same as they were over a 150 years ago.
In 1825 the mechanical press changed the glass industry forever! Iron casting
was considered the premier technology of the Industrial Revolution and made mass
production possible. But just how did they get the embossed text or design onto
the glass?
---------------------------
1. Information on line at: http://www.wheatonvillage.org
2. Available
reprints - 1971 by Pyne Press, Princeton
In 1875 Gustavus Storm received a patent for his design of a removable plate
that could be engraved with personalized lettering. It was an interchangeable
plate attached to the mold with a bolt.
Imagine two cast iron sides hinged together to form the overall shape, for
example any glass insulator shape. Now imagine a unique cast iron plate that can
be inserted and tightened into a precision cut slot in one or both outside
surfaces of the cast iron sides. When tightened the plate is snug and smooth on
the inside surface of the main wall of the cast iron mold itself. This was an
innovative design offered by Whitall, Tatum & Co.
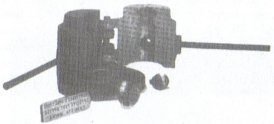
Courtesy, Gay LeCleir Taylor's companion catalog
to the exhibit Out of the Mold, Museum of
American Glass, 1990
Financially innovative because the overall shape of the produced glass from
the cast iron mold remained the same, however the consequence of this process
resulted in fewer employees, less design work, faster productivity and higher yield. The initial mold was only
different when an embossing plate, of unique text and/or design, was ordered by
a customer to be used on the now standard pressed-glass-product of the time.
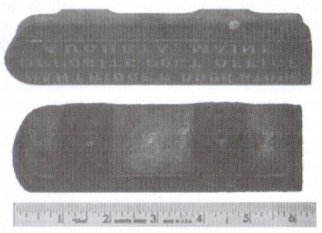
The entire slug plate is a MOLD! The cast iron slugs were blanks, sent to the
moldmaker and at that time the designs or text would then be precision tooled
into the plate. The embossing was not hammered onto the surface. Again, they
were made of cast iron, the same metal as the initial mold. The seam / space for
the slug plate is nil - though not seamless. A paltry shadow is apparent in the glass when using the slug plate.
One has to be determined to see the slug plate's shadowed outline with the naked
eye. However, some pressed glass orders from customers required the seam as an
integral part of the design as a whole.
Still, another important part of the mold is the mandrel or plunger. This is
the other "embossed" cast iron part. Anything pressed into and onto
the glass is indeed a mold. But how do they remove the plunger without tearing
the surface?
Typically, the plunger is tapered, with or without threads, text or designs.
(Today, cast iron is still the preferred metal, though stainless steel is now
used for the plunger.) Imagine pushing this plunger into the molten glass.
Without hesitation it can be turned the slightest and removed straight up with
no concern of glass temperatures³. The most secure part of the plunger is its
narrowest diameter - the tip first introduced or "plunged" into the
molten glass.
-----------------------------
3. Discussions with Don Friel,
Glass Artist at the Museum of American Glass
EDITOR'S NOTE: This short story with photographs was provided by Nance L.
Briscoe, not a collector or member, but an old friend of the hobby, now semi
retired from the Smithsonian Institution. Nance had been instrumental over the
years in providing access to hobbyists into the insulator collections, related
documentation and the eventual collaboration between NIA and the Institution. To
visit the Museum of American Glass call ahead for dates and hours (856)
825-6800.
Nance was one of the private parties invited by the Postal Service to inspect
two slug plate EC&M molds under investigation earlier this year. NIA
past-president Steve Marks reported on the investigation in an opinion published
in the September issue of Crown Jewels. The magazine invited opposing views, but
so far has received no opposing comments.
On the following page are additional color photos of the EC&M molds. The
mold pictured at the top of the page is made of flimsy, light weight steel.
Notice the excessive wear. The middle picture shows a large gap between the
copper slug plate and the steel mold. The bottom picture shows lines on an
EC&M insulator caused by the gap. Consider the differences between the
EC&M molds and the information presented by Nance from the Museum of
American Glass at Wheaton Village in Millville, New Jersey.
Again, Crown Jewels invites, and will publish, opposing views.
Another Opinion Casts Doubt on Molds

Note wear and etching of copper strip used for lettering.
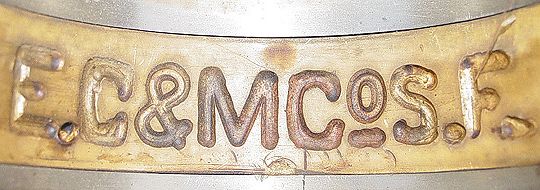
This copper slug plate is from a second EC&M mold. Notice the letters are
carved into the soft metal. Notice the gap between the copper slug plate and the
steel (not cast iron) mold. ( The image has been reversed for easier viewing.)
Below: Notice lines in glass caused by slug plate.
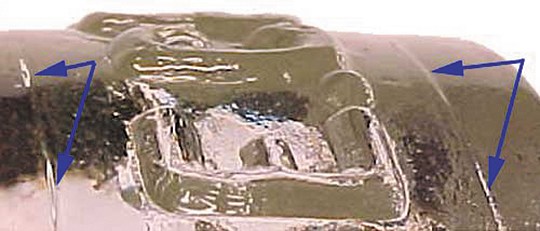
|